

Looking for a PhD project at The University of Melbourne?
​
We are offering several PhD projects that will be undertaken in partnership with industry and clinical partners. If you are interested in any of the projects listed below, please contact CMIT.
​
​
​
​
PhD Project
​
Stability of the glenohumeral joint after anatomic and reverse total shoulder arthroplasty
​
Anatomic total shoulder arthroplasty (TSA) is the established treatment for end-stage osteoarthritis of the glenohumeral joint; however, instability of the glenohumeral joint remains one of the most common and debilitating complications of this procedure. Reverse total shoulder arthroplasty (RSA) represents three-quarters of all shoulder arthroplasty procedures, and is known to increase the leverage and tension in the deltoid, recruit more of its fibres during abduction and flexion, and improve range of upper limb motion and glenohumeral joint stability. Dislocation and instability has been shown to account for up to 44% of all complications associated with RSA; however, its etiology, which is thought to involve prior surgery, bone deficiency, rotator cuff tears, and mechanical factors, has not been quantified to date. The objective of this project is to develop and validate computational models of the native shoulder and the shoulder after TSA and RSA, and to use these models to evaluate joint geometry, muscle loading, and stability of the glenohumeral joint after arthroplasty. The influence of prosthetic component selection and intra-operative placement will also be explored.

PhD Project
​
Muscle and joint function in the jaw and after prosthetic temporomandibular joint replacement surgery
​
The temporomandibular joint (TMJ) plays a pivotal role in the function of the lower jaw to enable chewing, talking, yawning, laughing and access to respiratory and digestive systems. Like the hip and knee, the TMJ may also be adversely affected by joint diseases such as osteoarthritis. In cases of end-stage osteoarthritis, as well as bone cancer and trauma, total joint replacement is the established treatment to restore jaw function. However, the design and evaluation of prosthetic joint replacements for the jaw has been greatly limited by the capacity to assess post-operative kinematics and evaluate internal muscle and joint loading. The aim of this project is to employ subject-specific computational modelling and experimentation to evaluate muscle forces, TMJ forces, bone stresses and occlusal loading during biting and chewing in 10 healthy controls, 10 pre-operative patients with end-stage TMJ conditions selected for total TMJ replacement surgery, and 10 aged-matched patients that have undergone unilateral total TMJ surgery at least 1 year prior. The results of this project will lead to improved design of prosthetic components for maxillofacial surgery, and an enhanced understanding of dynamic jaw muscle and joint function. The findings are expected to lead to improved implant design, including better TMJ motion and improved longevity.

PhD Project
A novel implantable distractor for the treatment of premature cranial fusion in children
Craniosynostosis is a birth defect that occurs when one or more of the joints (sutures) between the bones of a baby’s skull fuse prematurely. As the brain continues to grow, the head can become misshapen since it cannot expand in the normal directions. The increased internal pressure can result in visual and hearing loss, disrupted sleep, eating difficulties, or an impairment of early development combined with a significant reduction in IQ. If left untreated, craniosynostosis can result in death, especially when several sutures are affected. Surgical management of craniosynostosis involves cutting around the posterior aspect of the skull (craniectomy) to increase the skull volume and inserting distractors (adjustable plates) to repel the bone segments and increase the intracranial volume. Unfortunately, current distractor designs either reside internally to the scalp but do not provide capability to regulate the bone displacements that occurs during early development; or they provide variable bone displacement capability via external screws that protrude from the scalp and pose a high risk of infection or distractor damage. The objective of this proposal is to use computational modelling and experiments to develop the first internal skull distractor implant that is capable of providing safe and controlled separation of the skull bones and facilitate normal brain growth and skull formation in infants affected by craniosynostosis. The proposed new distractor design will reside under the scalp and deliver safe and accurate expansion to adjacent bone segments after bone craniectomy, facilitating normal cranial shape and volume gain in children affected by craniosynostosis. If successful, the project outcomes will help to minimise the very high mortality and complication rates of craniosynostosis surgery observed in Australia and worldwide.
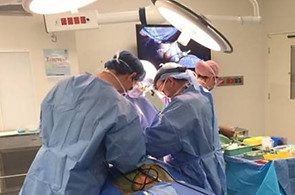
PhD Project
​
Computational Alloy Design for Additive Manufacturing of Orthopaedic Implants
​
The aim of this project is to design new high-performance orthopaedic metal composites and hybrids that can be fabricated by additive manufacturing. A key requirement for the design and deployment of such complex materials at minimal computational cost are top-down, performance driven, reduced order meta-models that incorporate a complete spectrum of process conditions and properties but that are sufficiently accurate to support engineering decision making. To overcome this barrier, we need to develop quantitative reduced order models that are based on multiscale simulations across different stages of the materials and product development process. The design method will follow a materials systems approach and use thermodynamic simulations to establish microstructural constraints and calculate the kinetic parameters; constitutive models to estimate the mechanical properties; and include a multi-objective genetic algorithm to optimize the chemical composition and the processing parameters.
​
​
Position requirements
​
An Honours degree in materials, mechanical or chemical engineering or a postgraduate degree in physics or chemistry. Interest and experience in computational science and engineering and the use of materials databases will be an advantage.

PhD Project
​
Design and optimisation of the micro-structure of a porous bone implant
Stress shielding is a phenomenon caused by the interaction of two materials with a vast difference in stiffness, in which the stiffer material absorbs the majority of the load. This effect is of particular importance for orthopaedic implants as conventional titanium implants present far larger stiffness than human bone. Consequently, the bone, which continuously models and remodels itself to adapt to mechanical loadings, is not stimulated anymore and goes into resorption, reducing its density and strength. This study aims to design and optimise novel porous implants to address the stress shielding and the consequent bone resorption. Of particular interests are auxetic structures. The project will evaluate different lattice topologies and their mechanical properties, including stiffness, Poisson’s ratio, strength, fatigue and fluid flow, and will optimise them for this application with a multi-objective approach. Numerical studies will be conducted with Finite Element methods, followed by experimental activities including mechanical testing on cadaveric specimens and lattice structures. This project will also take advantage of the rapidly changing technology in additive manufacturing (AM) to build lattice structures.
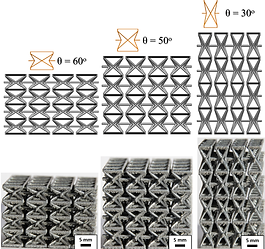
PhD Project
​
Developing a Measure – Model – Manufacture – Manage (4M) framework for point-of-care manufacturing for personalised orthopaedic implants and devices
​
Orthopaedic implants and devices are used to reduce pain and improve joint function in cases of end stage bone and joint conditions including osteoarthritis, congenital abnormalities, trauma and cancer. Recent disruptive technologies in biomechanical modelling and additive manufacturing (e.g. 3D printing) have potentially enabled implants to be built ‘on-demand’ and virtually tested, enabling a whole new era of point-of-care manufacturing of personalized implants with optimal function. This project will focus on developing a seamless computational framework based on the Measure-Model-Manufacture-Manage (4M) for point-of-care manufacturing. Comprehensive biomechanical measurements will be used to build patient-specific biomechanical models to represent the underlying physiology of the human body. The models will be used to analyse various scenarios that are too expensive or infeasible to perform on patients directly (e.g. loading an implant to failure in the human body). The aim in the measure-model stage is to optimise implant / device design that considers all the biomechanical information prior to manufacture using additive manufacturing (e.g. 3D printing). In manufacturing, material design is key. The 4M framework will incorporate material and structure optimisation algorithms to design implants that promotes bone/implant integration. Finally, the measure-model-manufacture becomes a reinforcing loop that improves patient management and outcome. For example, post-operative gait analysis information will be fed back into the 4M framework to help guide patient’s rehabilitation program.

PhD Project
​
Novel alloys for implants from hybridisation of microstructures by selective laser melting
Conventional metallic materials for implants are based on monolithic alloys designed for other applications. For example, the most commonly used Ti-6Al-4V is the dominant alloy for structures of aircraft. Consequently, their properties are often not desirable. The stiffness in Ti based alloys is much higher than that of bones, leading to stress shielding and loosened implants with time. Some alloy elements, such as Al and V, are harmful to the human body if dissolved. There is also a general lack of osteointegration between the implant and surrounding tissues. Although new alloys are being developed to overcome some of the deficiencies, they are limited by thermodynamics and conventional processing methods.
In this study, a new strategy will be pioneered in which microstructures of different alloys will be hybridised by selective laser melting, a major process used in additive manufacturing. The hybrid alloy will be designed based on the requirements for particular implants. The mechanical, physical and chemical behaviours will be characterised with a view to assessing the performances and understanding the interactions between various microstructures. The insight gained will be used to develop guidelines for the next generation of biomaterials for implants. It is expected that the project be closely aligned with the needs of the biomedical industry and hospitals, in particular those of the participating partners of ARC-CMIT.
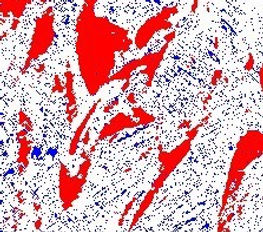